Innovations were brewing at one of the largest automatic plants in India. Gopal Namkeen’s ambitions were stymied by its reliance on traditional hosting, a lack of a barcode reading system, and non-integrated sales systems.
With the help of AWS Advanced Tier Services Partner, Aeonx, and its Greengrass technology solution powered by AWS, Gopal Namkeen automated these critical processes and integrated its disparate legacy systems into a cohesive technology stack. By focusing its resources on business strategy rather than on time-consuming manual processes, Gopal Namkeen has improved key marketplace KPIs and grown nearly 10x in the last year.
Accelerating with a rapid pace
With a reputable and trustworthy market position achieved through quality, reliability, and faith since 1994, Gopal Namkeen has one of the largest automatic plants spread over 75000 Sq.ft. in Rajkot. Gopal Namkeen’s crunchy, mouth-watering Snack Pellets are extremely popular in all age groups.
Gopal Namkeen faced significant challenges with being able to rapidly accelerate, scale, and improve its packing and dispatch architecture at the start of the pandemic. The problem could be attributed to three factors: traditional hosting, slow, independent systems that did not integrate well, and reliance on a labor-intensive, error-prone, non-integrated sales platform that was difficult to use for packing and despatch.
As Bipin Hadvani, Managing Director at Gopal Namkeen Group described it, “Our system and processes couldn’t maintain pace with our brand, catalog, and product range because we did not have the ability to move as aggressively as we would have liked.”
From day one, Gopal Namkeen made it clear that it wanted a complete picture of its systems, not views of different silos. They also required that the data be in JSON format for it to be imported into the portal.
Stepping into Integration and Automation
The project had to be done entirely remotely due to Covid-19 restrictions. In spite of this, the team managed to complete it in just two months. This is how Aeonx approached the task and completed it in such a short amount of time-
•Built a system that can read barcodes
•Developed a dispatching system that integrates sales orders
•Hosting of the solution within a development environment
•Testing by AeonX and Gopal Snacks team for end-to-end portal functionalities.
•DNS update for domain authentication and CName records.
•Provide live setup + support for 1 month after going live
We proposed AWS Greengrass technology to store the barcode data, which allows data to be stored locally in the event of an internet outage. This data can then be uploaded to the cloud once the internet is back up. Also, we created functionality in the portal to modify the time when packing vouchers are generated, which exports the data further to SAP through the REST API. Further, only approved sales order data is imported from SAP to the portal. In order to begin loading, the sales order is further matched against the dispatch line. If a different item that was not in the sales order is dispatched, the system is set up to automatically modify the order in SAP. Order status changes once the material is successfully loaded into the vehicle. Furthermore, the closed order data is sent to SAP using a REST API.
The barcode integration with the packing and dispatch system enables dealers the flexibility of ordering products and sharing information with the management, no matter where they are. With AWS, they can now automate key processes of their daily operations while tracking real-time data on SAP. “We are already seeing a 10-percent performance improvement and we are only halfway through implementation,” stated Bipin Hadvani, Managing Director, Gopal Namkeen.
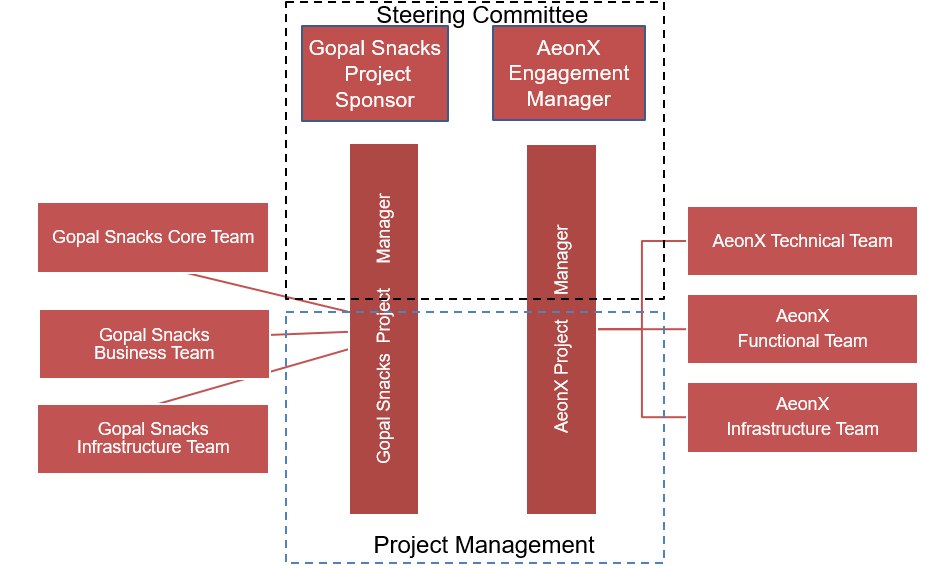